A dock is a major investment, so choosing the right material is crucial. Considering the primary uses of a dock and its floor conditions will influence the choice of material.
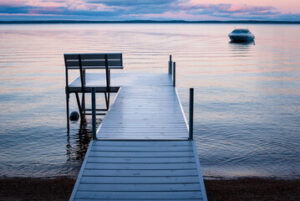
If a dock will be used for swimming or sunbathing — where bare feet will often contact the surface — then a non-splintering material is important. Decking materials range from cheap, pressure treated southern yellow pine to exotic hardwoods like Ipe or Cumaru.
A dock is a structure in the water that allows boats to be secured and accessed. It can be made of wood, concrete or metal and can vary in size and design. A dock can be used for recreational or commercial purposes. Dock building requires a lot of skill and knowledge in order to construct a sturdy and safe structure. A good dock builder is able to follow blueprint specifications and safety regulations. He or she is also able to work with tools like chain saws and drills, as well as heavy equipment like bobcats and trucks.
The materials used in Dock building are critical to the longevity of the structure. Choosing high-quality materials will ensure that the dock can withstand harsh weather conditions and constant exposure to water. Some popular dock building materials include composite decking, which is resistant to warping and rot, and galvanized steel hardware, which offers corrosion resistance in waterfront environments. In addition, using a durable and low-maintenance decking material like plastic lumber is becoming increasingly popular amongst dock builders.
Many dock owners choose to use pressure-treated pine wood for the framing of their structure. However, the chemicals used during the pressure treatment process can leach into the surrounding water and soil, leading to the eventual breakdown of the wood. Plastic lumber is a more eco-friendly option, and it is easy to work with. It also resists mildew and does not splinter.
Another common choice for dock materials is aluminum. While it is durable and lightweight, it is more expensive than other options. Additionally, it is more difficult to clean than other materials. Therefore, it is important to talk to your local Dock builder about the pros and cons of each material before making a final decision.
Besides material selection, it is also necessary to consider how the dock will be used. For example, incorporating bench seating into the design of the dock will eliminate the need to purchase additional furniture for the area. This will save both space and money.
Design
A dock is a structure that moors and supports a ship or any other water craft. A boat dock can have many different designs, depending on where it is located and what purpose it serves. The structure is very similar to a deck, with the same weight distribution and beams, but there are some differences that need to be taken into account when building a dock, such as the fact that it will be partly submerged in water.
Choosing the right design for your dock is essential to ensure that it meets your needs. It is important to consider what you intend to use the dock for and to make sure that it has enough space for your boats and any other amenities you may have in mind, such as fishing or sunbathing. You also want to ensure that the dock is sheltered from wind and water currents.
Before you start construction on your new dock, it is important to familiarize yourself with local regulations and permits. This will help you avoid any problems or delays that might derail your project. Additionally, it is a good idea to get the opinion of professionals, such as a licensed architect or engineer, before beginning the project.
A dock’s primary function is to berth ships and other vessels, but it is also used for maintenance, repair, and loading/unloading cargo. In order to ensure that the dock is at an adequate water level, it is necessary to regularly dredge the entrance channel and replace old, stagnant water with fresh seawater.
The defining feature of a pier is its elongated shape, extending into the water. These structures are generally made of concrete, but they can also be built from wood. Piers are a vital maritime structure, since they allow for mooring of large sea and ocean-going vessels, and are capable of surviving strong winds and tidal currents.
Docks are a great way to enjoy the water and the outdoors without having to leave your home. They are popular among families, and can be used for boat mooring, swimming, fishing, and entertaining. They can even be equipped with features like barbecues, fire pits, and seating.
Height
The height of a dock is an important consideration when designing and building your facility. A dock should be able to safely accommodate all truck and trailer configurations that are likely to visit the facility. This can be accomplished by determining the types and dimensions of trucks that will regularly visit the docks. This will help you to determine the maximum load height for the facility and the minimum dock door height.
A standard dock height is 48”, but many facilities customize this number. For example, a company that only services straight trucks may opt for a 42” dock height, while a company that only services container trucks will often install a 54” dock. This is done to match the truck shipping surface and warehouse floor heights for the most efficient loading of cargo.
Another factor to consider when deciding on the dock height is how much space will be needed for the trailers that will be servicing the facility. A good rule of thumb is to provide 1′ of space for each 10’ of trailer length. This allows for adequate maneuvering space for the trailers during reversing and positioning at the dock.
Typically, the truck bed will be 22” below or above the dock height depending on the type of freight that is being transported. The difference can be adjusted for with the use of a dock leveler, but it is also a good idea to design the facility with the ability to adjust the dock height based on unique trailer configurations.
In addition to the dock height it is also important to design the approach leading up to the bay door for a safe and functional loading operation. The apron should be constructed with concrete rather than asphalt to avoid depressions that can change the truck’s differential to the dock. This can lead to poor loading conditions and expensive repair costs later on.
The apron should be sloped so that the truck’s bumper is projected beyond the dock edge at full extension. This will protect the building from impact damage caused by a trailer that backs over the dock edge or fails to clear the dock edge during backing. For recessed approaches, additional projection can be achieved with the use of build-out blocks or a dock ramp.
Permits
The policies and regulations for dock permits vary from state to state, depending on local, county and city regulations. The regulations may also be based on homeowner association rules. It is important for property owners to know whether a permit is required before beginning construction. This can help them determine the best design and layout for their dock.
A dock is an enclosed water space that can be used for loading, unloading, repairing or building ships. It is usually built in a river, inland water body or seaport. Its main function is to protect ships from the effects of wind and water currents. Moreover, docks can also be used for storing cargo and equipment.
In some states, homeowners are allowed to build a private dock if it meets certain size and location restrictions. However, in many cases, a permit is needed to install or build a dock. A permit can also be required if the dock is located near an area frequented by manatees or seagrasses.
The requirements for a dock permit include the following:
An accurate dimensioned scale drawing of the proposed dock, including any other structures and utilities attached to it. This drawing should include the structure’s exact offshore location. It should also indicate the zoning district and show property lines. Detailed information regarding the construction materials and specifications should also be provided.
Any mooring, dock, pier, float or bulkhead that is sought to be constructed on or in Town waters must be submitted for approval to the Commissioner of Planning and Development. The application must contain a certified survey of the land where the dock is located and must comply with all other relevant zoning requirements.
It is also important to note that a dock cannot be built or modified in such a manner as to cause a safety hazard to navigation, obstruct the right of the public to pass along the foreshore between the mean high and low-water marks or impede the flow of navigable waters. It must also not interfere with the maintenance of adjacent beaches and existing permanent moorings and docks.